Customized Fabrication Process
Customized Fabrication
Custom metal fabrication is the process of taking raw materials and Designing, cutting, Forming, welding, Grinding/Cleaning and assembling them into a final product.
All kinds of industries rely on custom metal fabrication in NYC. This process produces parts and components of unique sizes and shapes, which customers then use for various Projects. While different MS steel manufacturers provide many of the same services, the quality of the finished product varies. Therefore, if you want precision, it is imperative to choose the right metal fabrication shop.
Both the standard and custom fabrication process of metal entails unique processes. In other words, metal fabrication consists of more than just one process, each working together to produce High-quality parts and components. This pro-production testing ensures the quality of the finished product and allows the customer to test the product in real world applications.
Following is a brief introduction as to what the various processes are and what WE involve.
All kinds of industries rely on custom metal fabrication in NYC. This process produces parts and components of unique sizes and shapes, which customers then use for various Projects. While different MS steel manufacturers provide many of the same services, the quality of the finished product varies. Therefore, if you want precision, it is imperative to choose the right metal fabrication shop.
Both the standard and custom fabrication process of metal entails unique processes. In other words, metal fabrication consists of more than just one process, each working together to produce High-quality parts and components. This pro-production testing ensures the quality of the finished product and allows the customer to test the product in real world applications.
Following is a brief introduction as to what the various processes are and what WE involve.
Designing
Before anything else, the project must be designed. While some fabricators still rely on hand-drawn diagrams, and those can be sufficient for basic projects, modern engineers generally use CAD (computer aided design) software, such as AutoCAD or Solid works. CAD allows for increased complexity and complete accuracy as they create and test models to exact specifications. Digital CAD files are also generally needed for metal Plasma/Oxi-Fuel cutting. For turning a piece of metal into a finished product, the fabricator needs a design.
Depending on the company needs, you can either provide the design or work with an engineer who can take your idea, specifications, and concept to produce the exact part or component required.
Depending on the company needs, you can either provide the design or work with an engineer who can take your idea, specifications, and concept to produce the exact part or component required.

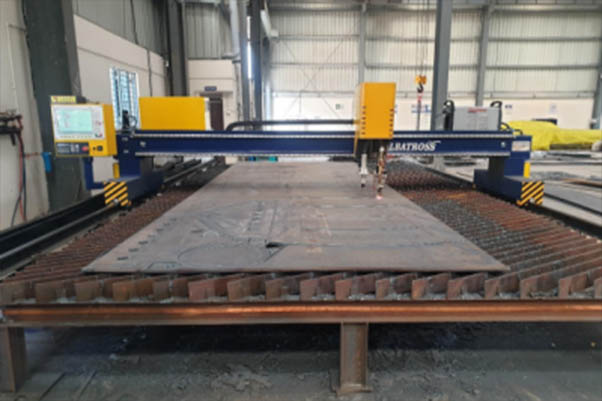
Cutting
CNC PLAZMA/Oxi-Fuel Cutting Machines – We use CNC PLAZMA CUTTING machine, which are known for producing precision Cutting metal products. For this, the design gets fed into a computer, and by using a state-of-the-art software program, the machine knows what to do. In response, the machine produces the Parts to 100 percent accuracy. Cutting is aspect of custom fabrication. There is a very low tolerance for error in any metalworking project, so choosing the right method for cutting the plate and sheet metal is very important.
The type of metal must be considered as well as the intended purpose and degree of precision required. The thickness and hardness of the metal is also an important factor to consider. Plasma cutting is the most precise way to cut sheet metal, especially when intricate designs or extreme accuracy is required. Plasma Capacity Up to 25 mm & Oxi-Fuel Capacity Up to 300 mm.
The type of metal must be considered as well as the intended purpose and degree of precision required. The thickness and hardness of the metal is also an important factor to consider. Plasma cutting is the most precise way to cut sheet metal, especially when intricate designs or extreme accuracy is required. Plasma Capacity Up to 25 mm & Oxi-Fuel Capacity Up to 300 mm.
Plate Rolling-Bending
This step includes bending to achieve the right shape by Rolling. After Rolling we make Shapes like Shell or Cylinder of Various Sizes as per Drg Requirement which includes Thk Capacity up to 50 mm x 2500 mm Pre-Punching.
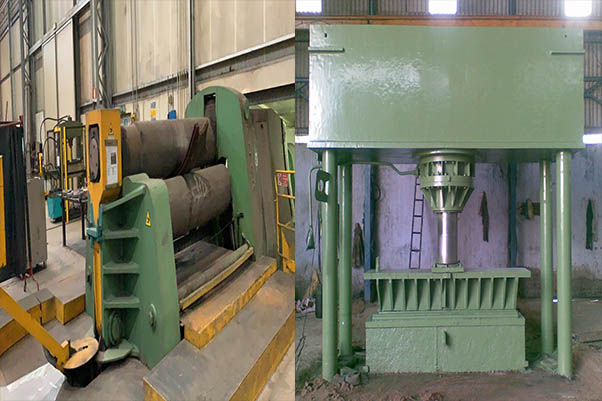
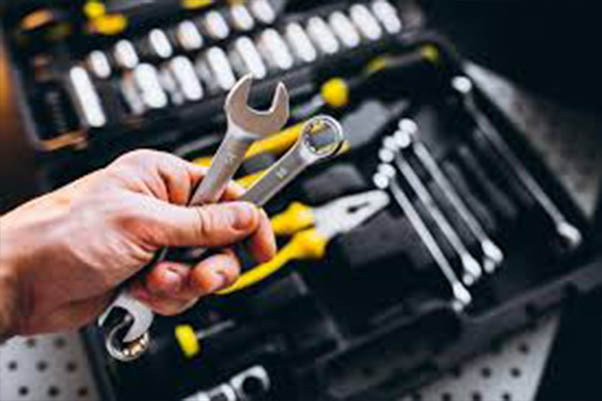
Fit-up (Assembling)
After the metal parts are formed into the correct shape, they must then be assembled into the proper configuration to make the final product. The separate parts are fitted together, and normally held in place by clamps until they are fused together. Then, the parts are put together with bonding, screwing, riveting, or most commonly, welding.
Welding
There are many different types of welds.
ARC Welding As Per WPS-PQR
Arc welding is a type of welding process using an electric arc to create heat to melt and join metals. A power supply creates an electric arc between a consumable or non-consumable electrode and the base material using either direct (DC) or alternating (AC) currents.
MIG Welding As Per WPS-PQR
MIG welding is a process in which a continuous solid wire electrode is fed through a welding gun and into the weld pool, joining the two base materials together. A shielding gas is also sent through the welding gun and protects the weld pool from contamination. In fact, MIG stands for metal inert gas. The technical name for it is gas metal arc welding (or GMAW), and the slang name for it is wire welding.
SAW Welding As Per WPS-PQR
SAW welding is a process in which a continuous wire electrode is fed through a welding Arm and into the weld pool, joining the two base materials together. A Flux is Use for Shielding and protects the weld pool from contamination. This Welding Process is used for Metal Thk 16mm to 200mm.
ARC Welding As Per WPS-PQR
Arc welding is a type of welding process using an electric arc to create heat to melt and join metals. A power supply creates an electric arc between a consumable or non-consumable electrode and the base material using either direct (DC) or alternating (AC) currents.
MIG Welding As Per WPS-PQR
MIG welding is a process in which a continuous solid wire electrode is fed through a welding gun and into the weld pool, joining the two base materials together. A shielding gas is also sent through the welding gun and protects the weld pool from contamination. In fact, MIG stands for metal inert gas. The technical name for it is gas metal arc welding (or GMAW), and the slang name for it is wire welding.
SAW Welding As Per WPS-PQR
SAW welding is a process in which a continuous wire electrode is fed through a welding Arm and into the weld pool, joining the two base materials together. A Flux is Use for Shielding and protects the weld pool from contamination. This Welding Process is used for Metal Thk 16mm to 200mm.
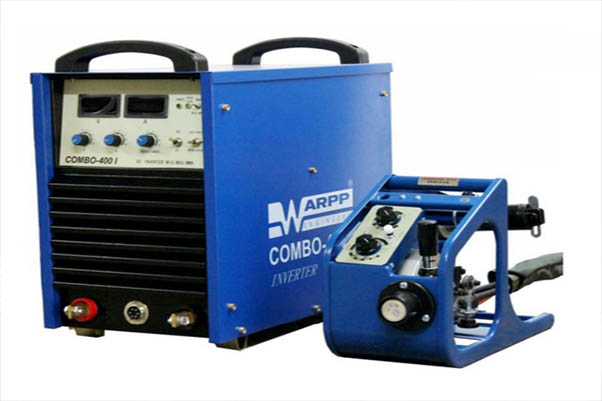
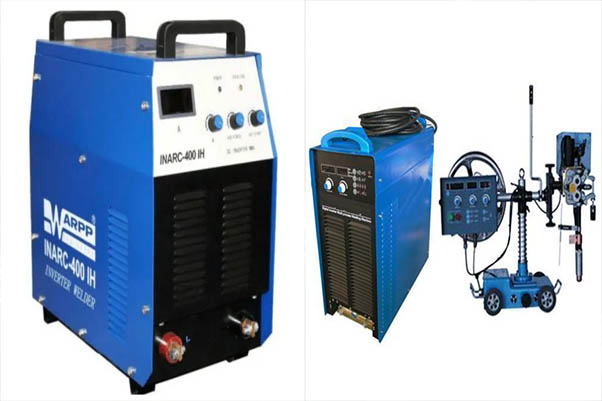
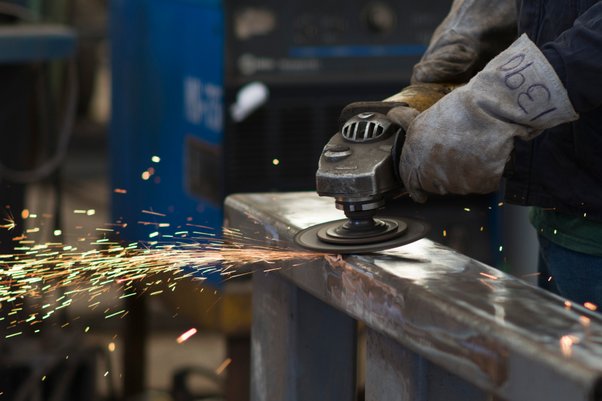
Grinding & Cleaning
After the Welding, Grinding Versus Finishing
They aren’t synonymous. In fact, each has a fundamentally different goal. Grinding removes material like burrs and excess weld metal, while finishing puts a finish on the metal surface. The confusion is understandable, considering those grinding with a large-grit wheel remove a lot of metal quickly and in so doing leave a “finish” of very deep scratches. But in grinding, scratches are just the aftereffect; quick material removal is the goal, especially when working with heat-sensitive metal like stainless steel.
Avoid Expensive Rework
Grinding, finishing, and cleaning for passivation testing on fabrication COMPONENTS. Passivation testing A COMPONENTS that isn’t finished properly creates some of the most expensive scrap and rework there is, so it makes sense for fabricators to take another look at their grinding and finishing departments. Improvements in grinding and finishing can help relieve major bottlenecks, improve quality, eliminate headaches, and, most important, improve customer satisfaction.
They aren’t synonymous. In fact, each has a fundamentally different goal. Grinding removes material like burrs and excess weld metal, while finishing puts a finish on the metal surface. The confusion is understandable, considering those grinding with a large-grit wheel remove a lot of metal quickly and in so doing leave a “finish” of very deep scratches. But in grinding, scratches are just the aftereffect; quick material removal is the goal, especially when working with heat-sensitive metal like stainless steel.
Avoid Expensive Rework
Grinding, finishing, and cleaning for passivation testing on fabrication COMPONENTS. Passivation testing A COMPONENTS that isn’t finished properly creates some of the most expensive scrap and rework there is, so it makes sense for fabricators to take another look at their grinding and finishing departments. Improvements in grinding and finishing can help relieve major bottlenecks, improve quality, eliminate headaches, and, most important, improve customer satisfaction.
Blasting & Painting
For the purpose of inspecting the blasted steel surface with cu slag abrasive, the respective. “Visual standards” can be utilized- We Type with Outsource Agency for Blasting and Painting Process
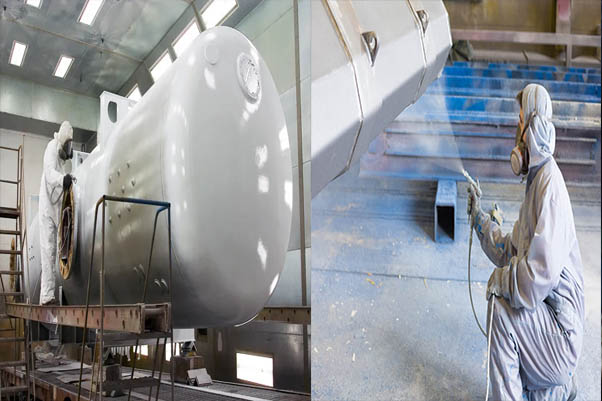